The Scientific Research Behind Porosity: A Comprehensive Guide for Welders and Fabricators
Understanding the complex systems behind porosity in welding is essential for welders and fabricators aiming for remarkable craftsmanship. From the make-up of the base products to the ins and outs of the welding process itself, a wide range of variables conspire to either aggravate or alleviate the existence of porosity.
Understanding Porosity in Welding
FIRST SENTENCE:
Evaluation of porosity in welding exposes crucial insights right into the integrity and top quality of the weld joint. Porosity, characterized by the presence of cavities or voids within the weld steel, is an usual concern in welding procedures. These spaces, otherwise properly attended to, can compromise the structural honesty and mechanical buildings of the weld, leading to prospective failures in the finished item.
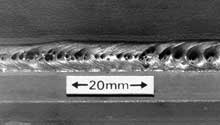
To spot and quantify porosity, non-destructive testing techniques such as ultrasonic screening or X-ray assessment are commonly used. These techniques enable the identification of internal defects without jeopardizing the honesty of the weld. By assessing the size, shape, and distribution of porosity within a weld, welders can make enlightened decisions to boost their welding processes and accomplish sounder weld joints.
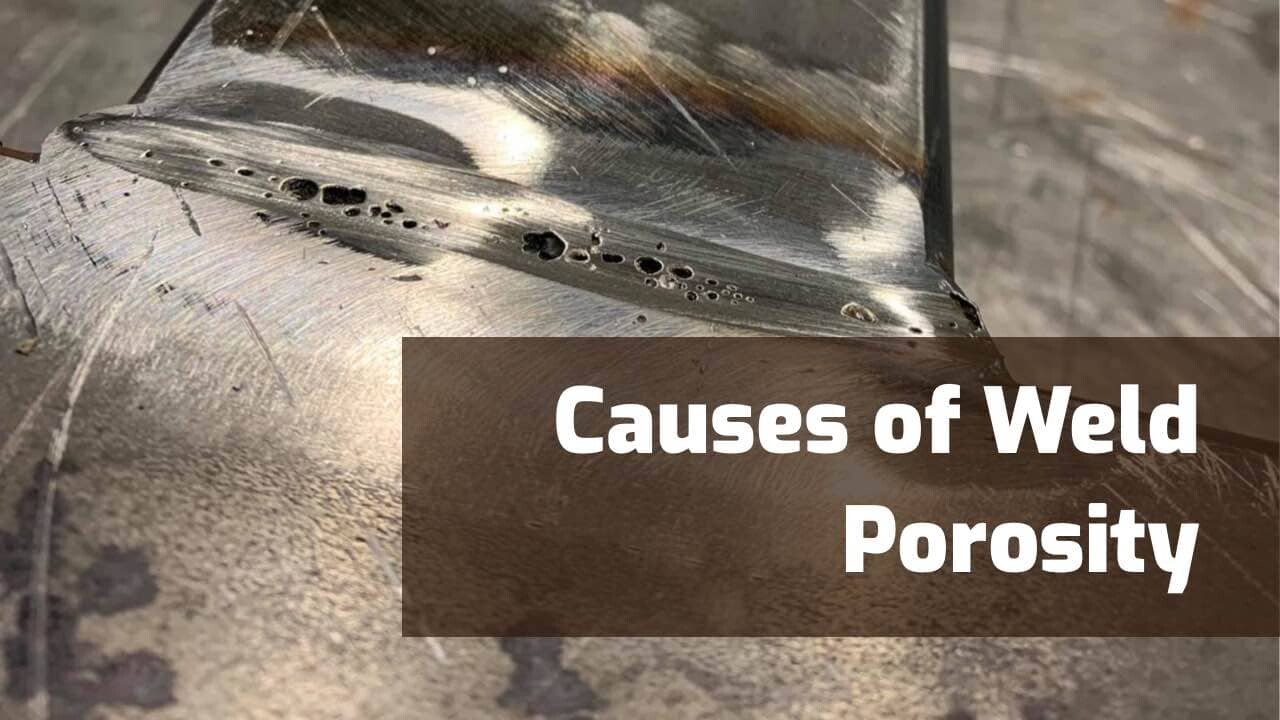
Aspects Affecting Porosity Development
The event of porosity in welding is influenced by a myriad of factors, varying from gas shielding performance to the complexities of welding parameter settings. Welding criteria, including voltage, present, take a trip rate, and electrode type, also effect porosity development. The welding technique employed, such as gas steel arc welding (GMAW) or shielded steel arc welding (SMAW), can influence porosity development due to variants in warmth circulation and gas coverage - What is Porosity.
Effects of Porosity on Weld High Quality
The presence of porosity additionally deteriorates the weld's resistance to corrosion, as the trapped air or gases within the gaps can react with the surrounding setting, leading to deterioration over time. Additionally, porosity can hinder the weld's capacity to stand up to stress or effect, more endangering the overall top quality and integrity of the welded framework. In vital applications such as aerospace, vehicle, or structural building and constructions, where safety and durability are critical, visit this site right here the detrimental results of porosity on weld quality can have extreme consequences, emphasizing the significance of lessening porosity through proper welding methods and treatments.
Techniques to Decrease Porosity
To improve the useful link quality of bonded joints and ensure architectural integrity, welders and makers employ certain techniques focused on reducing the development of voids and tooth cavities within the product throughout the welding process. One reliable approach to minimize porosity is to guarantee correct product preparation. This consists of comprehensive cleansing of the base steel to eliminate any type of impurities such as oil, oil, or dampness that might add to porosity development. In addition, making use of the appropriate welding specifications, such as the right voltage, existing, and take a trip rate, is crucial in stopping porosity. Keeping a consistent arc length and angle during welding also helps in reducing the chance of porosity.

Making use of the ideal welding method, such as back-stepping or using a weaving activity, can additionally assist distribute warmth evenly and reduce the possibilities of porosity formation. By executing these methods, welders can effectively decrease porosity and generate high-quality bonded joints.
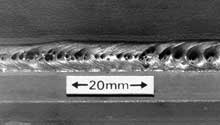
Advanced Solutions for Porosity Control
Applying sophisticated innovations and cutting-edge methods plays a pivotal duty in achieving exceptional control over porosity in welding processes. Furthermore, employing advanced welding strategies such as pulsed MIG welding or customized ambience welding can also aid alleviate porosity concerns.
One more sophisticated Recommended Site remedy includes making use of sophisticated welding tools. As an example, using tools with built-in features like waveform control and sophisticated source of power can enhance weld quality and minimize porosity threats. The execution of automated welding systems with precise control over criteria can substantially decrease porosity flaws.
Additionally, including advanced monitoring and inspection technologies such as real-time X-ray imaging or automated ultrasonic screening can help in discovering porosity early in the welding procedure, enabling prompt restorative activities. On the whole, integrating these advanced solutions can considerably enhance porosity control and enhance the general quality of bonded components.
Verdict
In final thought, comprehending the science behind porosity in welding is essential for welders and makers to generate high-quality welds - What is Porosity. Advanced remedies for porosity control can even more improve the welding procedure and make certain a strong and trusted weld.